Table of contents
- Introduction
- What is atomization technology?
- Types of Atomization Processes
- Gas Atomization
- Water atomization technology
- Centrifugal Atomization
- Ultrasonic atomization technology
- Industrial Applications of atomization technology
- Aerospace and Automotive
- Pharmaceuticals and Healthcare
- Food and Beverage Industry
- Energy and Environmental Sectors
- Benefits of Atomization Technology
- Improved Material Properties
- Enhanced Production Efficiency
- Customization and Flexibility
- Cost-Effectiveness
- Challenges in Atomization Technology
- Future Trends in Atomization Technology
- Focus on Nanotechnology
- Improvement of Additive Manufacturing
- Applying Eco Friendly Technologies
- Atomisation Technology: FAQs
- What is atomization?
- What industries use atomization technology?
- What are the different types of atomization?
- What are some possible benefits of atomization in manufacturing industries?
- What are the key areas for improvement in atomization technology?
- In what way does atomization impact the fuel efficiency of combustion engines?
- In what way is atomization implemented in drug delivery systems?
- What are the advantages of atomization to the environment?
- How does atomization work in the context of 3D printing technology?
- What is the future of atomization technology?
- Conclusion
Introduction
Almost all tasks require liquid mediums or liquids as handling tools. Atomization technology is changing industries by allowing liquids to be transformed into extremely tiny drops or fine mist with great accuracy. This technology has enabled almost all industries including aerospace, automotive, healthcare, and pharmaceuticals to perform their tasks in a much better and faster way.
This is rapidly advancing, particularly in industries focused on high-end materials. As a result, companies with expertise in fracturing are well-positioned for fast growth. Moreover, atomization is applied in processes that manipulate particle shapes, sizes, and dimensions, which directly impacts the final applications. Therefore, understanding how these attributes influence the end results is crucial.
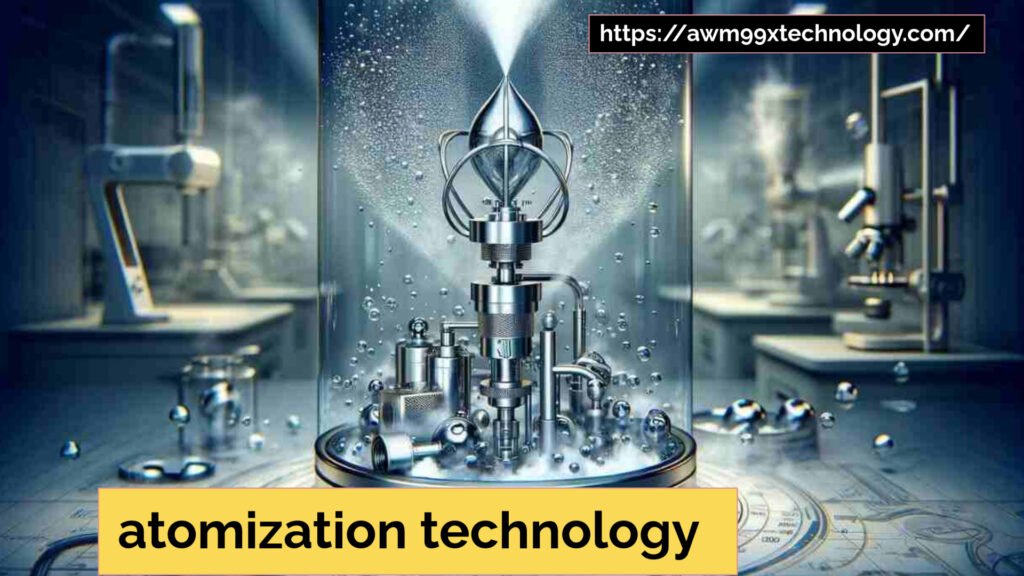
What is atomization technology?
Atomization is the process of transforming a beam of liquid into droplets of specific sizes using various methods and equipment. The size of these droplets can range from several tens of microns to nanometers, depending on the method used.
In this context, atomization focuses on controlling the size and shape of particles. It also controls the distance at which it disperses the particles. Industries widely use this technique to improve production processes, enhance material properties, and increase overall efficiency.
Atomization denotes the production of small droplets usually at a constant volume. An understanding of current concepts together with the utilization of atomization, the process of producing droplets from non dispersion sources, can be evolved. The utilization of atomization can be found in the following applications:
Tenka-zen (Japan) and Dewolf (Netherlands) are associated with Kedalion in the provision of atomization services. Atomization allows for the production of metal powders that can be feedstock for other processes such as:
Medical Aerosols: Used in nebulizers and drug delivery systems.
Types of Atomization Processes
Based on droplet forming method, Atomization processes can be divided into 2 major types:
Gas Atomization
Process: A high-speed gas such as air or nitrogen is blowed to break a liquid or molten medium into these fine droplets.
Applications: The production of metal powders, Additive manufacturing, Metal Injection Moulding. Especially useful for manufacturing spherical metal powders that have applications in 3D printing and powder metallurgy.
Water atomization technology
Process: This technique is a direct immersion process. A stream of water quenches the molten metal breaking it into droplets.
Applications: Production of metal powders, especially for those industries where a lower cost method is required. It’s widely used in production of Aluminum; steel and other non ferrous metals.
Centrifugal Atomization
Process: A rotating single disc or drum throws the molten material outward, breaking it into droplets. As it moves outward, the material continues to break into smaller droplets, making it easier to manipulate.
Applications: Making mechanical parts with fine powders in the additive manufacturing or casting industries. Used for high-performance alloys and materials which rely on a fine and consistent powder size.
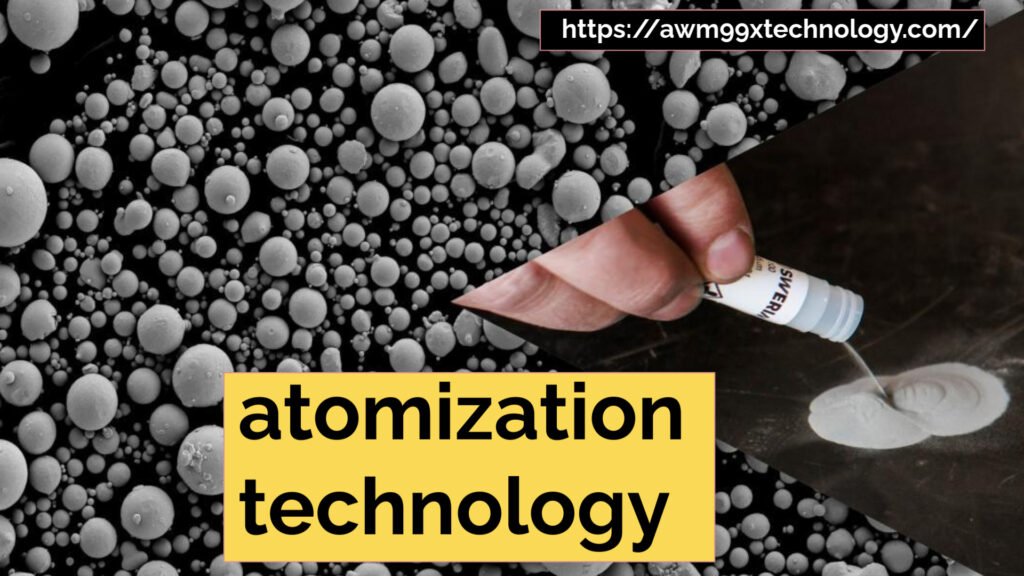
Ultrasonic atomization technology
Process: High frequency sound waves create vibrations which break the liquid into droplets.
Applications: Used in medical devices for controlled drug delivery, fuel injection and advanced cooling systems in engines.
Industrial Applications of atomization technology
Multiple industries use atomization technology for various applications. For example, several industries that have adopted atomization include the following:
Aerospace and Automotive
Atomization plays a vital role in producing metal powders for additive manufacturing (3D printing), which then create complex parts and components. It also atomizes fuels for combustion engines, promoting complete combustion and improving engine performance while reducing emissions.
Applications: Metal 3D printing, powdered metallurgy, combustion fuel injectors, and combustion systems.
Pharmaceuticals and Healthcare
In the pharmaceutical industry, atomization is quite useful for nebulizers where the active ingredient is effectively atomized into very fine powder like particles so as to enhance bioavailability and effectiveness of the drug.
Applications: Nebulizers (drug delivery systems), pharmaceutical spray drying, vaccine development.
Food and Beverage Industry
Atomization allows the consistent manufacturing of food ingredients in powdery form like milk powder, coffee, and flavorings, as the processes result in uniform particle size and consistency in the products.
Applications: Spray drying of liquid food, powdered or liquid food flavoring, and foods mixed with water or other dehydrated products are common applications of atomization.
Coatings and Paints
Atomization is regularly utilized in the formulation of paint and coatings, and adhesives where there is a need for control over particle size and distribution that can affect the characteristics of the coating or the finish.
Applications: Painting with powder coating, applying spray paints and performing surface coating.
Energy and Environmental Sectors
Atomization improves fuel efficiency in combustion processes and turbines. It breaks fuel or chemicals into fine droplets. This enhances water treatment by improving chemical absorption and dispersion.
Applications: Turbine fuel atomization, industrial water treatment, and waste treatment.
Benefits of Atomization Technology
The technology is adopted in atomization in different industries for fuel savings, environmental protection and elevated performance especially atomization of diesel or fuel oil.
Improved Material Properties
It produces particles with high shape uniformity. This improves the properties of end products. For example, the uniformity of metal powder used in 3D printing or pharmaceutical manufacturing ensures better performance. It also guarantees consistent and reliable final products.
Enhanced Production Efficiency
Atomization provides effective control on particle size and distribution which minimizes the wastages of materials and improves efficiency of manufacturing processes. Inhere, in the fields of aerospace and automotive where high level of accuracy is expected, it certainly ensures that components satisfy these rigid requirements.
Customization and Flexibility
Several atomization processes help to switch to the most appropriate technique to address the specific requirements of customers building in more flexibility in design and production. From making fine powders for 3D printing applications to creating uniform droplets in drug delivery systems, it has got an edge for atomization.
Cost-Effectiveness
The most notable benefit of atomization technology is cost savings. It enhances material utilization and reduces waste. Additionally, process engineering improves transformation efficiency, leading to shorter production cycles. This saves both time and money.
Challenges in Atomization Technology
Quite a number of challenges come in accepting atomization including:
Material Properties
In atomizing processes, physical properties of materials like viscosity, surface tension, and melting point are critical factors affecting atomization.Worst still some materials might necessitate use of special facilities or alterations on the equipment to achieve optimum atomization outcomes.
Equipment Costs
The relatively higher prices of good quality atomization equipment remain a setback concentrate in those operations which require precision. In addition to these, running and upkeep of such systems will entail a slant cost of training, skilling, maintaining, and energy.
Consistency and Control
Maintaining a consistent particle size and droplet distribution can be challenging, especially with complex materials or during scale-up. Variability in droplet size affects product quality, so precise control systems are necessary to manage this variability.
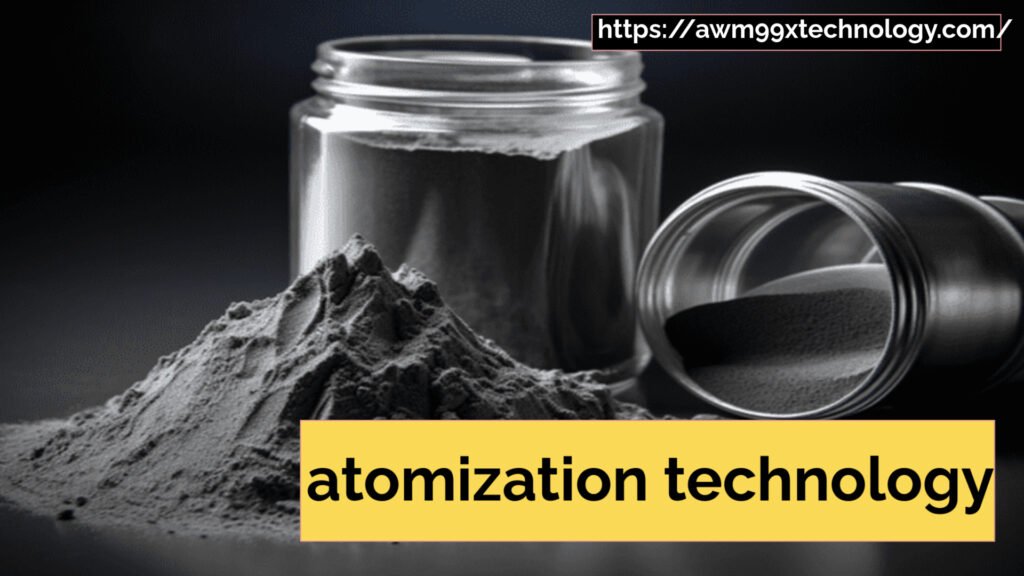
Future Trends in Atomization Technology
The future of technology is bright as there is a likely prospect of improvement of the material and the process that will broaden its applications. Some significant trends are:
Focus on Nanotechnology
A trend is emerging in the use of nanomaterials in atomization operations. This approach creates finer particles and more advanced materials. It is especially important in electronics, medicine, and energy storage.
Improvement of Additive Manufacturing
The ascent of additive manufacturing (3D printing) is stimulating the need for fine metal powders made through atomization. As 3D printing continues to unfold, the process of atomization will be significant in the supplying of materials needed.
Applying Eco Friendly Technologies
Atomization is applied in clean production processes. For instance, in the automotive and energy industries, it serves to enhance fuel efficiency, minimize emissions, and enable clean technology.
ALSO READ THIS BLOG : TECH ETRUESPORTS: THE NEW ERA OF SPORTS ANALYTICS AND INTERACTION
Atomisation Technology: FAQs
What is atomization?
A trend is emerging in the use of nanomaterials in atomization operations. This approach creates finer particles and more advanced materials. It is especially important in electronics, medicine, and energy storage.
What industries use atomization technology?
Atomization finds application in diverse industries including:
Aerospace: This is for metal powder preparation and for burning atomizer to enhance combustion performance.
Automotive: In the production of parts and perfection of fuel injectors.
Pharmaceuticals: When designing drug delivery devices that are nebulizers, and for spray drying processes of powdered medications.
Food and Beverage: In the preparation of instant powders such as milk powder and powdered flavorings.
Energy and Environmental: This is a fuel atomizer for turbines and for efficient combustion and water treatment.
Coatings and Paints: Application of atomization is in the production of uniform powder coatings and sprays for various industrial purposes.
What are the different types of atomization?
In general, the following types of atomisation are relatively common:
Gas Atomization: Make use of high pressure gas to break molten material into tiny droplets.
Water Atomization: This method entails water in which the molten material is transformed into tiny droplets by cooling and solidifying the droplets.
Centrifugal Atomization: In summary, this method’s basic principle consists of the spinning of a molten liquid in the high speed with the aim of creating droplets.
Ultrasonic Atomization: Application of high frequency sound waves in the generation of small droplets that are medically and other specialized uses.
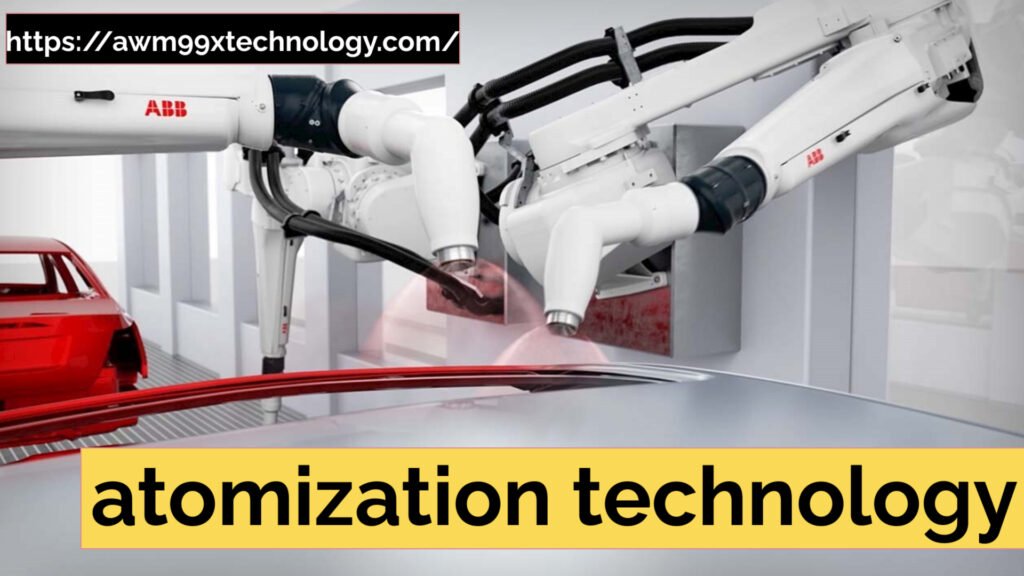
What are some possible benefits of atomization in manufacturing industries?
The crucial points of advantage of the atomization technology are:
Enhanced Quality of Materials: Is responsible of making by creating rounds of the particles with the aims of improving the qualities and the performance of the end product.
Enhanced Effectiveness: Ensures proper sizing and distribution of particles hence cutting down on material wastage and increasing the rate of output.
Money-saving: Minimization of waste is achieved because optimum raw materials are used leading to efficient processes hence reducing production costs.
Versatility: There are no limitations to the application of atomization due to the fact that it can be applied to many materials and for many purposes ranging from the pharmaceutical to the aerospace industry.
What are the key areas for improvement in atomization technology?
Whilst there are many benefits attributable to the use of atomization in practice, there are also clearly some disadvantages. These include:
Conformability or Material Compatibility: There are possibilities that some materials could be hard to atomize because of the viscosity, surface tension and other such physical characteristics.
High Cost of Equipment: Atomization systems tend to be quite costly in terms of purchase and maintenance. This is so especially in cases where industries are precision oriented.
Uniformity: It is usually easy to achieve uniform size of droplets and spray patterns in a small sized business. Large scale production however poses a challenge.
Power Consumption: There are atomization processes such as gas atomization that tend to consume a lot of energy.
In what way does atomization impact the fuel efficiency of combustion engines?
Atomization in a combustion system is useful to get fuel injected in the form of very fine droplets before the combustion. This provides a better air-fuel ratio resulting in a better combustion process. Therefore, engines operate effectively and have higher outputs while emitting lesser pollutants. In aerospace and automotive industries, atomization also improves engines and reduces the amount of fuel consumed.
In what way is atomization implemented in drug delivery systems?
Atomization processes in the pharmaceutical industry include the application of pulverizers and inhalers to produce mists of drug formulation suitable for lung administration. The inhalation lung drug delivery technique (ILD) allows fine particles generated through ultrasonic and pneumatic atomization to improve the bioavailability of drugs, enabling more medication to reach the desired site within the body. It is particularly effective when managing some respiratory diseases such as asthma and COPD.
What are the advantages of atomization to the environment?
Atomization reduces waste and improves fuel efficiency, enhancing material use and lowering emissions in industries like powder metallurgy and energy production.
Energy-Efficient Manufacturing: First of all, the atomization process used in spray drying or coating is helpful in minimizing material usage or waste and thus minimizing the emissions caused by the energy usage in industrial works.
How does atomization work in the context of 3D printing technology?
Atomization creates fine metal powders for 3D printing, ensuring precision and durability in industries like aerospace, automotive, and healthcare.
What is the future of atomization technology?
It is believed that in the future, the technology of atomization will have the following features:
Nanotechnology: Atomization technology targeted towards nanomaterials will be key to enhancing the development of electronics, energy storage devices and medical equipment’s innovations.
Integration with Additive Manufacturing: Since 3D printing has been gaining traction, the need for the finest powders to be used in such a process will guarantee that it is atomization which will be widely used.
Sustainability: It is anticipated that atomization processes will further reduce waste and pollution thus the overall sustainability of a manufacturing practice is enhanced.
Advanced Control Systems: More accurate control systems will expand the possibilities for droplet size and diameter improvement, enhancing the atomization’s material quality.
Conclusion
The influence of atomization technology on manufacturing processes is evident in many industries. Atomization has become a necessary device as it raises material quality strategy, bolsters efficiency enhancement and offers added flexibility to companies that operate in an ever-changing environment. The costs of equipment and challenges of material properties are drawbacks but relative to the benefits, they are minimal.
With the changing global trends, industries will have to adapt more advanced technologies which means atomization will continue to dominate the manufacturing landscape, providing futuristic solutions for the needs of the ever-changing market. Atomization is one of the best solutions for global aerospace, healthcare, automotive, and pharmaceutical sectors, it optimizes production and improves products.
1 thought on “Atomization Technology: A Comprehensive Guide to Its Industrial Applications”